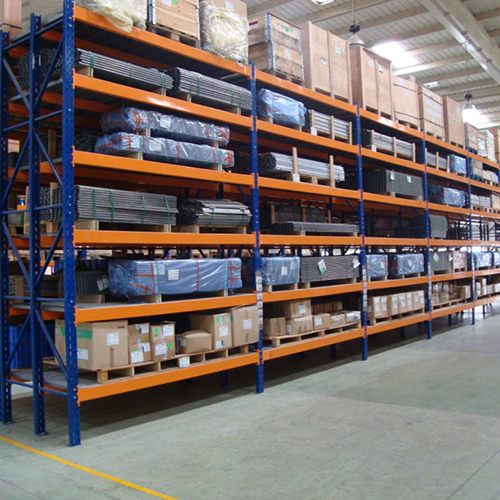
Make Certain Racks Are Fully Load-bearing
When storing hefty coils, devices, and dies, it’s hard to plan for future weights, forms, and sizes. Some heavy duty rack systems will cover the distance of the shelf and rest on both steel support beams, however others won’t. When this holds true, it is essential to have a storage space rack created to be completely load-bearing, no matter where the material sits.
For instance, when holding slim coils, it’s typical practice to position the coil in the middle of the cradle to make sure that it doesn’t rest over one or both rack beams. To compensate, rack makers should change the angle, breadth, and thickness of cradle supports to manage the greatest load at the weakest point– the center of the cradle. Coil cradles also should be created so that the coils constantly rest on a level surface area instead of the sides of the cradles, which can lead to serious creasing or flattening.
Select Strong Materials for Your Heavy Duty Racks
The product and form of your heavy duty racks will substantially influence performance. The material used in the columns, arms, and shelf beams will also impact your heavy duty racking. Make certain that you are getting the appropriate product for the load kinds and weights you need.
Hot-rolled steel metal shelfs are ideal for taking care of high loads. They are likewise very resistant to harm from forklifts and other equipment. Cold-rolled steel, though, may not be optimal for high load heavy duty metal racking. Damages to this type of steel may jeopardize the framework, and reduce its weight capability.
Ensure Beams and Arms Are Fully Bonded
When a forklift operator unintentionally presses the forks up under a shelf arm, he generates an uplift weight condition that can be particularly harmful to an arm that isn’t completely bonded. A forklift with a simple 6,000-lb. loading volume can dramatically damage an arm, specifically if it does not have any weight stashed on it. Welding around the entire boundary of the I-beam at the connector plate enhances support to protect the arm from these uplift weights.
While it’s uncommon to locate cantilever racks that aren’t totally welded, you can inspect the weld to make sure. If it’s not completely welded, the location more than likely to be missing out on a weld is the bottom of the flange or the side of the web. The shelf should have a fillet weld that is continuous around the arm material and connector plate. While some elements of the weld are hard to inspect after painting, you can examine to see to it the weld is placed evenly at the origin of the joint between the arm and plate material.